Plastic injection molding is an efficient process that produces high-quality parts quickly. It is also affordable for large-volume production runs.
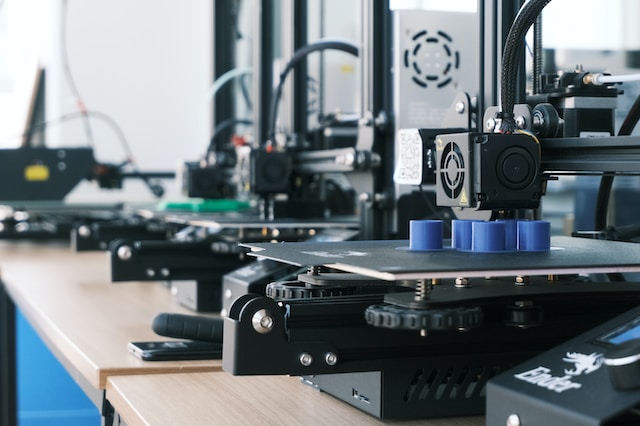
The first step in the process is to fabricate the tooling. This includes the barrel, which holds the reciprocating screw, and the plastic granules. Heater bands also surround the barrel to melt the plastic.
Customization
A plastic injection mold is a precision tool that creates the shape of your product. It is typically constructed in two halves that meet at the parting line. Each half contains the geometry, surface texture, or polished surfaces you design for your product.
If you are planning to add fasteners to your injection molded product, you can choose to model threads directly on the part or include a threaded insert. Threaded inserts can be made of metal or plastic.
Selecting a suitable plastic depends on the design, application, and environmental exposure. Considerations like shrink rates and viscosity are essential as well. For example, if your plastic injection product will be used in a cold environment, you should consider using a flexible plastic such as PP or HDPE.
Sustainability
Sustainable manufacturing is more than just a trend—it’s an essential industry component. Embracing environmentally conscious improvements helps manufacturers become more efficient, competitive, and profitable.
Plastic injection molding is a highly accurate process that produces minimal scrap plastic, making it more eco-friendly. Injection molding also uses various recyclable materials, reduces energy consumption, and minimizes transportation emissions.
From flexible electronics to sterile medical devices, the precision and durability of plastic injection molds are vital for several applications. Injection molding has even helped to revolutionize automobile production by replacing metal parts with lighter, more durable polymers that still meet strength and performance requirements. This allows for greater design freedom and improved fuel economy. The result is a better vehicle for the environment and its passengers.
Durability
Durability is a critical factor in choosing the materials that go into products. Durable materials are more cost-effective in the long run as they reduce the need for maintenance and repair and can also reduce waste.
Durable plastics can withstand harsh environmental conditions, such as humidity and extreme temperatures. Additionally, UV additives can protect plastic injection molded components from sun damage.
Injection molding produces little waste from the sprue and runners, and any unused plastic can be recycled. This makes injection molded parts highly sustainable.
Ease of Manufacture
Injection molding uses a machine injects melted plastic into durable, temperature-controlled metal molds. This allows for the production of large volumes and reduces per-unit manufacturing costs.
One family injection mold can produce multiple parts of the same design using interchangeable inserts into the central cavity (also known as the “B side”). The B side typically contains functional features such as bosses, ribs, and snap-fits.
Avoid sharp corners on your design to prevent stress concentrations that can cause weaker parts. Also, a draft angle should be added to vertical walls to allow the ejection of molded plastics from the mold more easily. Lastly, avoid thick sections of the wall, as these increase manufacturing time and cost. These tips can significantly lower your total injection molding production cost.
Low Cost
Plastic injection molding is an excellent option for products that require high-volume production and consistency. It also produces fewer defects than other manufacturing processes, saving costs.
The cost of a plastic injection mold depends on its size and complexity. Larger molds can cost more, requiring a more giant injection machine and handling equipment. The number of cavities in the mold also impacts cost, as each additional cavity increases the amount of material, machining time, and design work required.
Experts can help minimize costs by selecting the best material for your application, designing a more efficient mold, and minimizing waste. Using suitable materials will also reduce operating costs, as they are less likely to degrade over time and can provide superior durability.